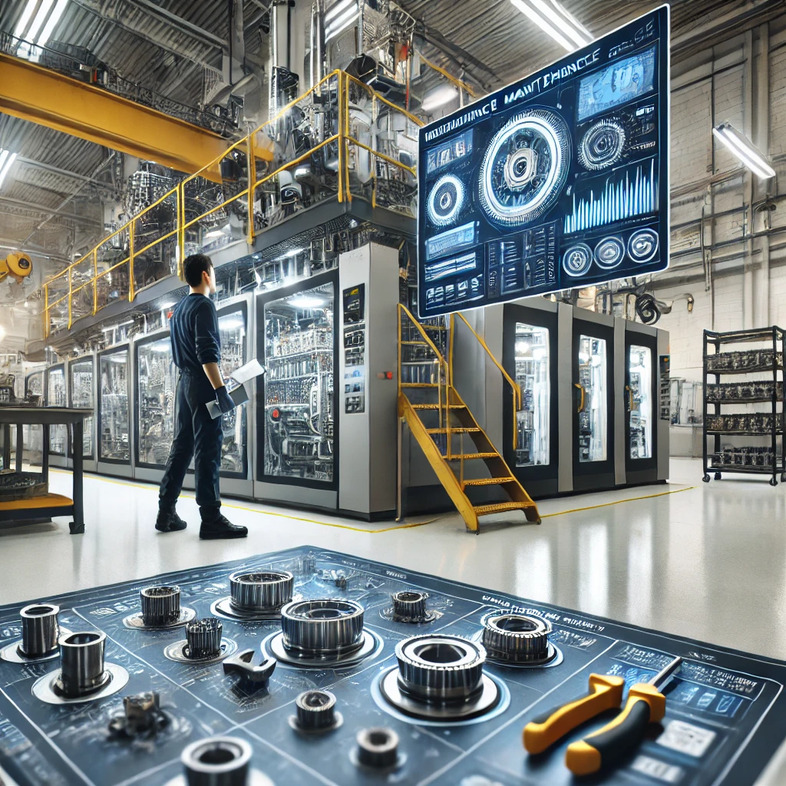
Techniques to Enhance the Lifespan of Equipment After Sales
To ensure long-term performance, maximize return on investment, and minimize downtime, companies need to focus on strategies that enhance the lifespan of equipment after sales. Proper maintenance and smart management play a crucial role in achieving these goals. Here are several effective techniques to prolong the life of equipment post-purchase.
1. Predictive Maintenance
One of the most efficient ways to ensure the longevity of your equipment is through predictive maintenance. Unlike traditional scheduled maintenance, predictive maintenance uses sensors, data analytics, and machine learning algorithms to monitor the real-time condition of equipment. By identifying potential failures before they occur, you can schedule repairs at the most convenient times, reducing unexpected breakdowns.
Benefits:
- Early detection of issues
- Reduced unplanned downtime
- Lower maintenance costs
2. Implement Regular Inspections and Servicing
Routine inspections can help identify wear and tear before it leads to costly breakdowns. Ensure your team follows a strict inspection checklist that covers all critical components of the equipment. Timely servicing as per the manufacturer’s recommendations will keep the machinery running efficiently and help extend its operational life.
Key areas to monitor:
- Lubrication of moving parts
- Electrical components
- Cooling systems
- Hydraulic systems
3. Use High-Quality Spare Parts
Using genuine, high-quality spare parts ensures that your equipment operates at optimal performance levels. Cheaper, substandard parts may save money upfront but can lead to significant losses over time due to frequent replacements, breakdowns, and increased wear on other components.
Tips:
- Build relationships with trusted suppliers
- Maintain an inventory of essential spare parts
- Track and replace worn parts promptly
4. Proper Training for Operators
A well-trained operator is essential to the longevity of your equipment. Ensure that all users are adequately trained to operate the machinery safely and efficiently. Operator errors due to improper use are one of the leading causes of premature wear and tear. Regular training sessions and refreshers can help maintain operational efficiency.
Focus on:
Safe operating procedures
Troubleshooting basic issues
Regular equipment calibration
5. Monitor Equipment Usage
Overuse or improper use of equipment can significantly shorten its lifespan. By monitoring equipment usage and ensuring it is used within recommended operational limits, you can reduce wear and tear and ensure that it remains in optimal condition for longer.
Techniques:
- Implement usage tracking systems
- Avoid running machinery at maximum capacity continuously
- Rotate equipment usage to distribute wear evenly
6. Effective Lubrication Management
Friction is the enemy of most mechanical systems. By ensuring proper lubrication, you can drastically reduce friction, preventing wear and tear on critical components. Implementing a regular lubrication schedule based on manufacturer guidelines ensures optimal machine performance and longevity.
Best Practices:
Use the right type of lubricant for each component
Monitor lubrication levels regularly
Replace lubricants as necessary based on operating conditions
7. Environmental Control
The environment in which your equipment operates plays a significant role in its longevity. Dust, humidity, and temperature fluctuations can have a detrimental effect on machinery. Ensuring that your equipment is housed in a controlled environment can help mitigate these factors.
Considerations:
Use dust filters and regular cleaning protocols
Maintain stable operating temperatures
Monitor for corrosive elements in the environment
8. Document and Analyze Maintenance History
Keeping detailed records of your equipment’s maintenance history helps in understanding performance trends and predicting future issues. This data-driven approach allows you to spot patterns in failures or repairs and make informed decisions regarding upgrades or replacements.
What to track:
- Frequency of repairs
- Parts replaced
- Downtime due to maintenance
- Root causes of failures
9. Upgrading Components and Retrofits
As equipment ages, newer, more efficient components become available. Retrofitting or upgrading outdated parts can help extend the life of older machinery. These upgrades often improve efficiency, reduce energy consumption, and enhance overall performance, breathing new life into existing equipment.
Upgrade examples:
- Implementing energy-efficient motors
- Upgrading control systems
- Installing modern sensors for enhanced monitoring
10. Establish Strong After-Sales Support
Building a strong relationship with the equipment supplier can be invaluable. Suppliers often provide after-sales support, including maintenance packages, spare parts availability, and expert technical advice. Ensuring you have access to this support can significantly enhance the longevity of your equipment.
Benefits:
- Access to expert technicians
- Regular software updates and patches (for digital systems)
- Prioritized access to spare parts
Conclusion
Prolonging the life of your equipment after sales is not just about following basic maintenance schedules. It requires a comprehensive approach that includes predictive maintenance, training, environmental control, and regular upgrades. By implementing these techniques, companies can significantly improve the performance and durability of their machinery, reduce operational costs, and maximize their return on investment. With the right practices in place, your equipment can remain a valuable asset for many years to come.