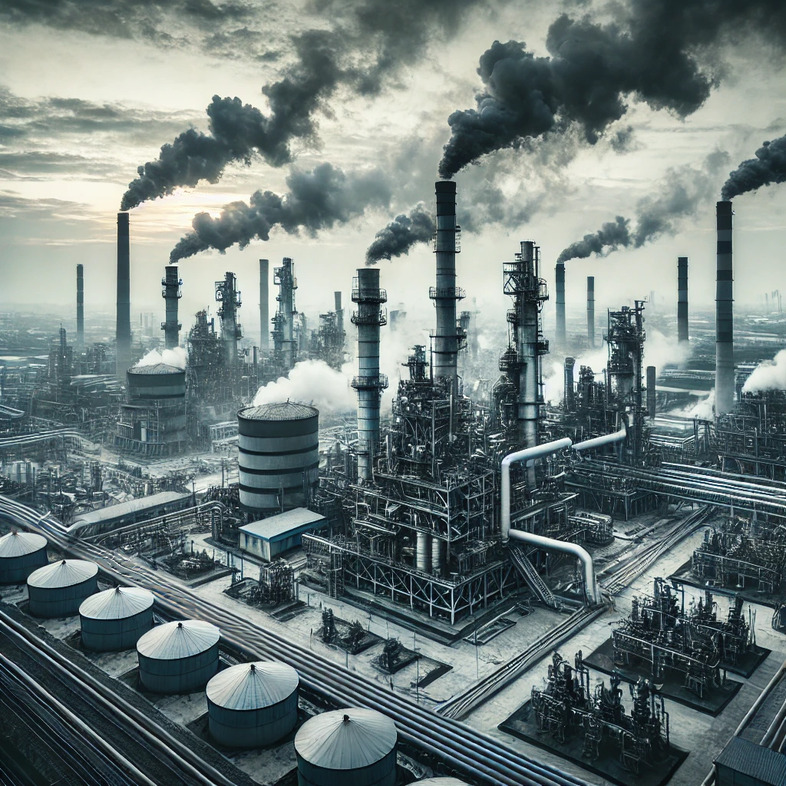
The Link Between Maintenance and Carbon Emissions
By Vikram Pol, Operations manager at Linecare.tech
Machines that are not well-maintained often operate below optimal efficiency, requiring more energy to perform the same tasks. For example, studies show that poorly maintained equipment can consume 15-20% more energy compared to well-maintained systems (U.S. Department of Energy). This increased energy consumption directly translates to higher carbon emissions, especially if the energy source is fossil-fuel-based.
For many manufacturing facilities, energy accounts for a significant portion of operational costs. According to the International Energy Agency (IEA), the industrial sector is responsible for 24% of global carbon dioxide (CO2) emissions. A significant portion of these emissions comes from equipment operating inefficiently due to lack of maintenance. By neglecting regular upkeep, businesses inadvertently contribute to a larger carbon footprint, undermining global efforts to combat climate change.
Key Areas Affected by Poor Maintenance
Energy Inefficiency: Equipment that requires more power due to wear and tear not only drives up operational costs but also increases emissions. According to the Carbon Trust, machinery that isn’t properly maintained can lead to increased energy use of up to 30% in some cases, particularly in energy-intensive industries like steel manufacturing and cement production.
Increased Downtime and Waste: Machines that frequently break down or require premature replacement generate more waste. Manufacturing new parts or entire machines involves significant energy use. For instance, the production of industrial machinery emits an estimated 1.8 metric tons of CO2 per machine, based on data from the European Environment Agency (EEA). Replacing machinery more often due to poor maintenance can compound these emissions.
Extended Production Times: Inefficient machinery often leads to slower production cycles, requiring plants to run longer to meet targets. The U.S. Environmental Protection Agency (EPA) estimates that equipment running below optimal efficiency can increase operational time by up to 10%, further driving up energy consumption and emissions.
The Solution: Proactive Maintenance
Implementing a proactive maintenance program can drastically reduce these issues. Regular inspections, timely repairs, and predictive maintenance technologies ensure that machines run at optimal efficiency, reducing energy consumption by up to 20% and prolonging their lifespan (Carbon Trust). By maintaining equipment in peak condition, manufacturing plants can lower their carbon emissions, reduce waste, and contribute to sustainability goals.
In addition to environmental benefits, proactive maintenance also saves costs by improving energy efficiency and minimizing downtime, creating a win-win scenario for both businesses and the planet.
Conclusion
For manufacturing industries, reducing carbon emissions is not just a matter of switching to renewable energy sources—it also requires a commitment to proper machine maintenance. By ensuring that equipment operates efficiently, companies can lower their energy consumption, reduce waste, and play a crucial role in fighting climate change. Effective maintenance could cut global carbon emissions by 15-20%, highlighting the essential role of operational efficiency in reducing industrial CO2 output (U.S. Department of Energy).