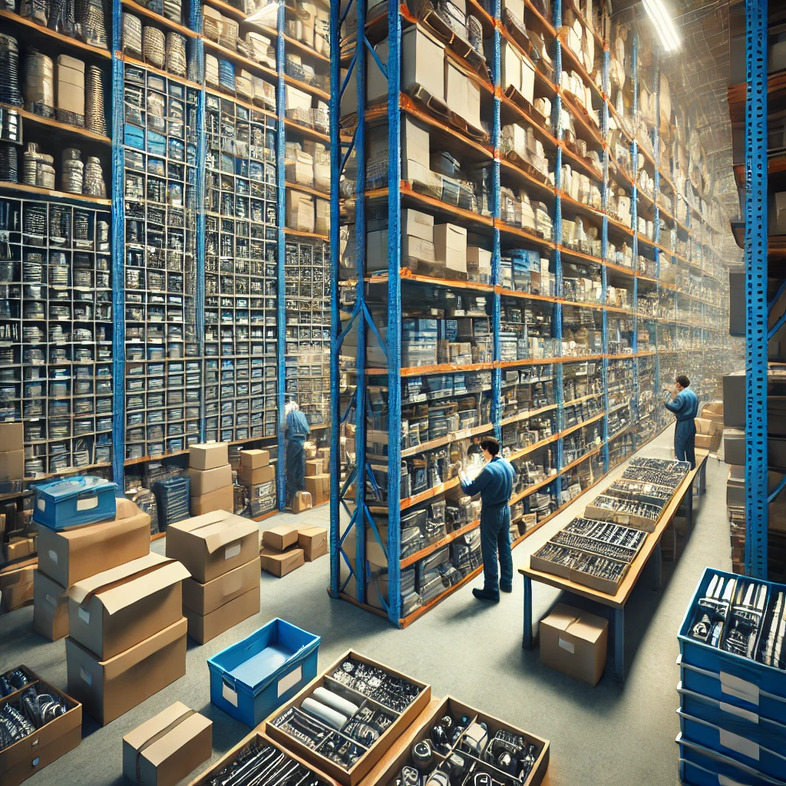
The Role of Inventory in Maintenance
By Vikram Pol, Operations Manager at Linecare.tech
Inventory management plays a vital role in maintenance operations by ensuring that necessary spare parts, tools, and materials are readily available when equipment requires repairs or routine servicing. This helps maintenance teams reduce downtime, enhance productivity, and prolong the lifespan of machinery and equipment. Properly managing inventory allows maintenance departments to work efficiently, avoid production delays, and improve cost-effectiveness.
One of the key aspects of inventory in maintenance is minimizing downtime. When equipment breaks down or requires preventive maintenance, having the right spare parts in stock ensures repairs are completed quickly. Without a proper inventory system, delays can occur if parts need to be ordered or sourced externally, potentially halting production for extended periods. An effective inventory system ensures that maintenance technicians have access to the parts they need, reducing the time equipment is offline and improving operational efficiency.
Inventory also supports preventive maintenance efforts. Preventive maintenance is scheduled maintenance based on equipment usage and wear patterns to prevent unexpected failures. Having an organized inventory system allows maintenance teams to have the right parts and materials available for these routine tasks. This minimizes the risk of equipment breakdowns, improving reliability and reducing the need for emergency repairs.
Another significant benefit of inventory in maintenance is cost control. Overstocking can tie up capital and take up valuable space, while understocking can lead to urgent orders, which are often more expensive due to rush fees. A well-structured inventory system helps balance stock levels, ensuring that the maintenance team has what they need without excessive surplus. It also helps avoid last-minute purchases, which can disrupt maintenance schedules and inflate costs.
Additionally, inventory tracking enhances resource allocation. Maintenance teams can keep track of which parts are used most frequently, helping them anticipate future needs and ensure that critical items are always on hand. It also provides insight into equipment performance, identifying trends in wear and tear, and enabling better decision-making for equipment upgrades or replacements.
In addition, Linecare.tech offers a parts section that provides manufacturers with access to necessary spare parts, further aiding in smooth and timely maintenance. This service ensures that manufacturers can minimize downtime and maintain high productivity levels by having the right parts at their disposal. Inventory tracking also aids in anticipating future needs, ensuring critical parts are always available.
In conclusion, inventory management is essential for the smooth functioning of maintenance operations. By ensuring timely availability of parts and materials, it helps minimize downtime, supports preventive maintenance, and optimizes costs, ultimately contributing to better operational efficiency and equipment longevity.