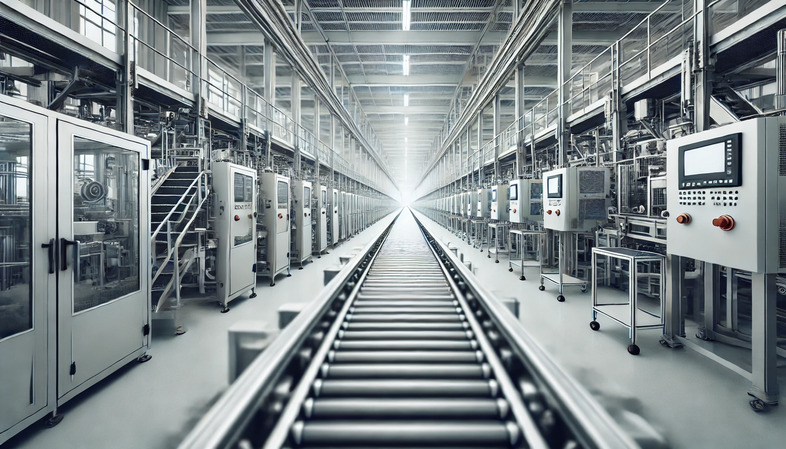
Top 5 signs your manufacturing line needs immediate maintenance
In the fast-paced world of manufacturing, ensuring smooth and efficient operations is critical to staying competitive. Equipment failure or unexpected downtime can lead to significant financial losses, production delays, and missed deadlines. To avoid such disruptions, it’s important to recognize early signs that your manufacturing line needs immediate maintenance. Addressing these issues before they escalate can save time, money, and stress. Here are the top five signs that indicate your manufacturing line requires urgent attention.
1. Unusual Noises or Vibrations
One of the earliest and most noticeable signs of equipment trouble is strange noises or vibrations. If machines start making grinding, squeaking, or knocking sounds, it’s often a clear indication that something isn’t functioning correctly. These noises may be caused by worn-out bearings, loose components, or misaligned parts. Vibrations can also signal problems such as imbalanced machinery or defective parts. Left unchecked, these seemingly minor issues can lead to significant damage, potentially requiring costly repairs or replacements.
2. Inconsistent Product Quality
When a manufacturing line isn’t operating at peak efficiency, it often reflects in the quality of the products being produced. If you notice a decline in product quality — such as variations in size, shape, or finish — this could be a sign that equipment calibration is off or certain components are wearing out. Inconsistent output may also point to problems with process control, which can affect the overall reliability of your operations. Addressing these issues promptly can prevent defective products from reaching customers, saving your reputation and reducing waste.
3. Increased Downtime
If you find that your manufacturing line is experiencing more frequent stoppages, either for repairs or unexplained reasons, it’s a clear signal that immediate maintenance is needed. Increased downtime can result from a range of issues, including overheating motors, faulty sensors, or software glitches in automated systems. These interruptions not only halt production but can also have a ripple effect on your entire operation, delaying shipments and creating bottlenecks. Performing a thorough inspection to diagnose and fix the root cause of downtime can restore operational flow.
4. Higher Energy Consumption
A sudden spike in energy usage can be an indication that your equipment is no longer running efficiently. When machinery has to work harder due to wear and tear, malfunctioning parts, or blockages, it consumes more energy. This not only increases your operational costs but also places unnecessary strain on the equipment, potentially leading to breakdowns. Monitoring energy consumption can help you identify when maintenance is needed before more serious damage occurs.
5. Excessive Wear on Parts
Regularly inspecting your equipment for signs of excessive wear and tear on parts is crucial for maintaining the longevity of your manufacturing line. Components like belts, bearings, gears, and seals naturally wear out over time, but when you start seeing signs of premature wear, it’s often a sign of underlying issues such as misalignment, improper lubrication, or overuse. Replacing worn parts promptly can prevent more extensive damage and avoid unscheduled downtime.
Conclusion
In manufacturing, prevention is always better than cure. By staying vigilant and recognizing these early warning signs, you can take swift action to maintain the efficiency of your production line and avoid unexpected breakdowns. Implementing a proactive maintenance schedule, using data from your equipment to identify patterns, and training your staff to spot these issues can help keep your operations running smoothly. Remember, timely maintenance not only saves costs in the long run but also ensures that your equipment continues to perform at its best.